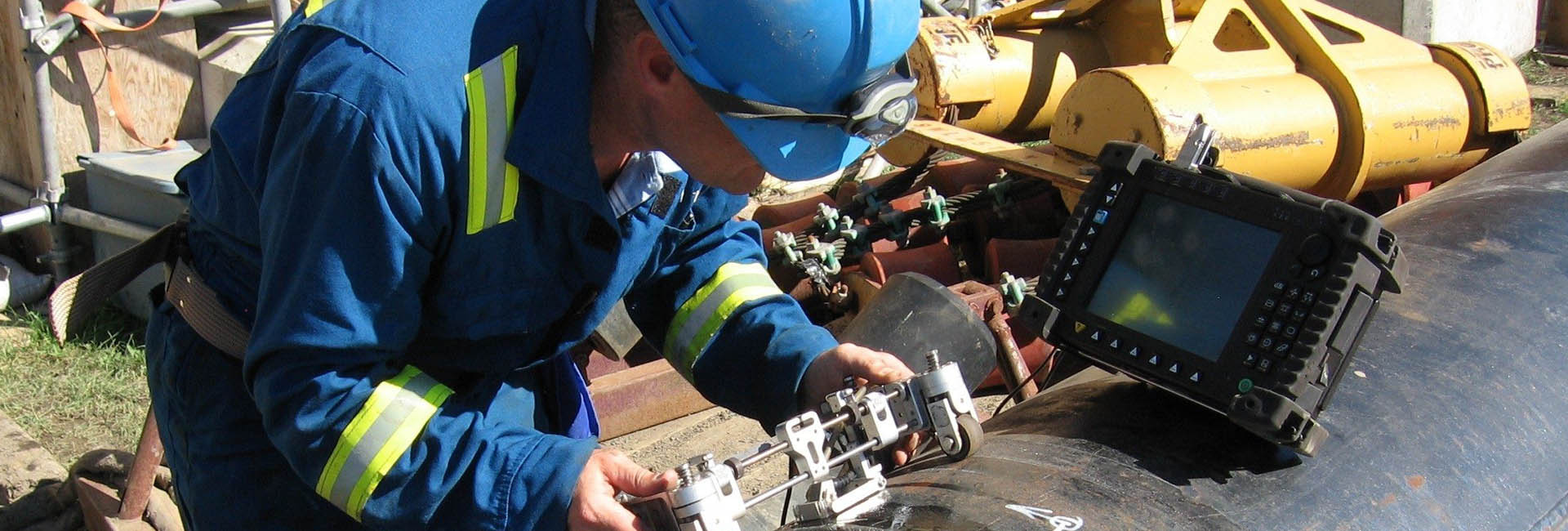
Оборудование НПС «РИСКОМ»
Переносная система УЗК СКАРУЧ
Установка используется для ручного и механизированного ультразвукового контроля качества сварных соединений и основного металла со скоростью продольного сканирования 0.5 - 1.0 м/мин вдоль сварного шва или участка основного металла.
"СКАРУЧ" работает в режиме автоматической фиксации и расшифровки результатов контроля (АФ и РРК) при ручном сканировании системой преобразователей, а также в режиме ручного дефектоскопа (толщиномера) общего назначения.
Функциональные особенности:
- осуществляет 16 различных схем прозвучивания на каждом миллиметре контроля;
- обнаруживает внутренние дефекты (поры, шлаковые включения, непровары, трещины и др.);
- идентифицирует дефекты по характеру (объемные, объемно-плоскостные, плоскостные);
- оценивает параметры дефектов (длину и развитие по глубине);
- проводит толщинометрию основного металла по сканируемой поверхности с шириной участка 65 мм;
- автоматически отслеживает уровень акустического контакта с изделием;
- автоматически устанавливает и корректирует параметры УЗК с поправкой на шероховатость;
- осуществляет самоконтроль работоспособности электроники и акустической системы;
- автоматически фиксирует, запоминает и расшифровывает результаты дефектоскопии;
- производит передачу результатов контроля в память подключаемого компьютера;
- распечатывает результаты контроля с помощью подключаемого принтера;
- имеет автономное питание.
Параметр Ед. изм. Значение:
- дискретность регистрации датчика пути мм 1
- дискретность регистрации параметров дефекта мм 1
- дискретность регистрации толщины мм 0,1
- измерение параметров дефекта сварного шва с погрешностью по длине мм ±1
- измерение параметров дефекта сварного шва с погрешностью по глубине развития мм ± 0,5
- определение координат дефекта вдоль шва с погрешностью от пройденного пути % не более 1
- минимально выявляемый дефект мм 0,8...1,0
- скорость УЗК м/мин до 1
- количество каналов 8
- количество схем прозвучивания 16
- частотный диапазон МГц 1,0...10,0
- максимальное усиление по каждому каналу дБ 90
- диапазон регулировки усиления дБ 85
- максимальная глубина прозвучивания (продольные волны) мм 10000
- время непрерывной работы от аккумуляторов (6 шт.x1,2В) ч 8
- стандартный диапазон рабочих температур °С -10...+35
- расширенный диапазон рабочих температур °С -20...+50
- время установления рабочего режима мин 1
- габариты дефектоскопа мм 200х225х90
- вес дефектоскопа (с аккумуляторами) кг 3,5
Функциональные возможности:
- «Заморозка» изображений и запись их в память (до 1000 изображений с сопутствующей информацией)
- Измерение координат «Х», «Y», толщины.
- Наличие ВРЧ.
- Количество точек регулировки ВРЧ – до 8.
- Индикация температуры
- Отображение заряда аккумуляторов
- Объем использованной и оставшейся памяти
- Время и дата
Состав установки "СКАРУЧ" состоит из следующих узлов:
- малогабаритный восьмиканальный дефектоскоп "СКАНЕР";
- многоэлементный акустический блок (АБ);
- механическое приспособление (МП) с датчиком измерения пройденного пути;
- информационный кабель (ИК).
Принцип работы установки в автоматическом режиме:
Работа установки осуществляется в 16-ти тактовом режиме. Каждый такт осуществляет заложенную схему контроля. Для каждого такта заранее установлены и хранятся в памяти прибора: уровень чувствительности (согласно требованиям действующей НТД); положение и длительность строба (согласно контролируемой толщине и расстоянию до шва); амплитудные пороги фиксации дефекта и определения его размеров по сечению.
На каждом миллиметре пути фиксируются амплитуды во всех 16-ти тактах, которые затем обрабатываются в дефектоскопе.На каждом миллиметре происходит прозвучивание всего сечения контролируемого металла одновременно с двух сторон от шва (для стыковых и нахлесточных соединений, имеющих двухсторонний доступ), а при перемещении оператором механического приспособления с акустическим блоком - всего контролируемого участка (сварного соединения и основного металла). Временнaя система стробирования и микропроцессорная обработка принимаемых каждым из ПЭП сигналов от дефекта позволяет идентифицировать тип дефекта (объемный, плоскостной, объемно-плоскостной). Определение параметров дефекта происходит путем сравнения всех принятых от него сигналов и определения в цикле тактов максимальных (для эхо- методов) и минимальных (для зеркально-теневых) амплитуд на каждом миллиметре пути. При толщинометрии производится измерение значений толщины каждым из четырех ПЭП, входящих в акустический блок. Толщинометрию проводят сканированием акустическим блоком по контролируемому участку.